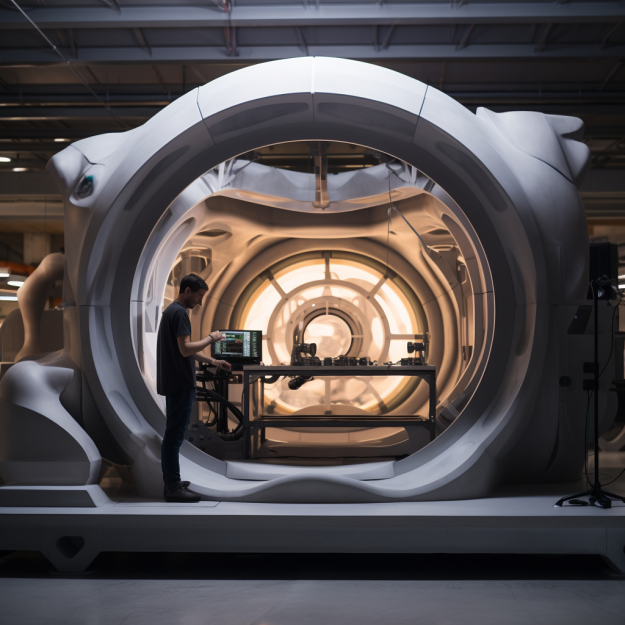
In the world of electronics and mechanics manufacturing, precision is more than just a buzzword—it's a necessity. This precision becomes incredibly crucial during the prototyping phase, where every detail matters and can determine the success or failure of the final product. At Hemargroup, we've honed an advanced approach to prototyping, leveraging state-of-the-art technology, such as diverse 3D printers and printing techniques, and a team of skilled professionals committed to delivering excellence.
Why Prototyping Matters
Before we delve into our unique approach at Hemargroup, it's essential to understand why prototyping is such a pivotal step in the manufacturing process, regardless of the industry.
Breathing Life Into Concepts
At its core, prototyping is the process of bringing ideas to life. It gives designers, engineers, and stakeholders a tangible model for an idea or concept. This shift from the theoretical plane to a physical one is critical as it opens up the design to comprehensive analysis. A prototype offers an opportunity to interact with a design physically, allowing for invaluable feedback and insights into functionality, aesthetics, and overall viability.
Testing and Refinement
With a prototype in hand, engineers can start the vital process of testing and refining the product. It provides a platform for us to verify design assumptions and identify possible improvements. This iterative process is integral in ensuring the end product not only meets the design objectives but also delivers the intended user experience. Through this rigorous testing and refinement, prototypes evolve, inching ever closer to a finalized, market-ready product.
Evaluating Manufacturing Methods
Prototyping also plays a critical role in the logistical aspect of product development - the manufacturing process. It offers us a chance to evaluate different manufacturing methods, assess their feasibility, and choose the most efficient and cost-effective one. This evaluation is particularly crucial in electronics and mechanical engineering, where the manufacturing process can directly impact the product's functionality and reliability.
Identifying Potential Issues
Another essential benefit of prototyping is its ability to help identify potential issues and roadblocks ahead of time. Be it ergonomic concerns, material selection, assembly issues, or potential design flaws; a prototype can reveal problems that may not be evident in a digital design environment. Catching these issues during the prototyping phase can save significant time, effort, and resources that would have been spent on rectifying them during the production stage.
Gaining User Insights
Finally, prototypes are an invaluable tool for gathering user feedback. End-users can interact with the prototype, providing real-world insights and highlighting potential areas for improvement from a usability perspective. This feedback is crucial to ensuring that the final product aligns with user needs and expectations, leading to a successful product launch.
In essence, prototyping is the essential bridge between the abstract concept and the concrete, market-ready product. It ensures that the transition from idea to product is smooth, informed, and strategically aligned with both technical specifications and user needs. The power of prototyping cannot be underestimated, and at Hemargroup, we harness this power to its fullest potential to deliver exceptional products to our clients.
Incorporating Electronics and Mechanics
The realm of product development has always been one of fusion—ideas blending with technology, design interfacing with functionality, and in our specialized field, electronics meeting mechanics. Hemargroup's advanced approach to prototyping actively embraces and enhances this confluence of disciplines, bringing electronics and mechanics together in harmony.
Beyond the Circuit Board: The Interplay of Electronics and Mechanics
Today's electronic devices are rarely purely electronic; most have significant mechanical components that play crucial roles in their operation and user experience. Consider the tangible elements like buttons, casings, mounts, and even cooling systems—all these components require mechanical design and precision engineering to function in concert with the electronic heart of the device.
Understanding this intricate interplay between electronic and mechanical aspects, Hemargroup has developed a comprehensive approach to prototyping that gives equal importance to both.
A Seamless Blend: Our Prototyping Workflow
Our prototyping workflow is built around a seamless integration of electronics and mechanics. We start by mapping out the interdependencies between electronic components and mechanical elements in the design. This allows us to understand how changes in one can affect the other, ensuring a truly integrated design process.
Our interdisciplinary team, comprising both electronic and mechanical engineers, works collaboratively through each phase of the prototyping process. Their expertise enables us to optimize the design for both electronic functionality and mechanical reliability, ensuring the overall product works flawlessly and efficiently.
The Role of Cutting-Edge Technology
A significant aspect of our unique approach is the utilization of cutting-edge tools and technology, like diverse 3D printing techniques, in the creation of mechanical components.
3D printing allows us to rapidly fabricate precise and complex mechanical parts that would otherwise be time-consuming or even impossible to produce using traditional manufacturing techniques. From casings and connectors to intricate gear systems, we can create high-quality mechanical prototypes that perfectly integrate with their electronic counterparts.
Furthermore, the versatility of 3D printing allows us to experiment with various materials and manufacturing processes, thus giving us more freedom to innovate and push the boundaries of what's possible in product design.
3D Printing at Hemargroup: The Edge in Prototyping
Over the last decade, 3D printing has emerged as a technological revolution, completely transforming the landscape of prototyping. At Hemargroup, we've enthusiastically embraced this technology, recognizing its potential to amplify the quality, speed, and precision of our prototyping process.
Revolutionizing Prototyping with 3D Printing
The advent of 3D printing has introduced an unprecedented level of flexibility and precision into the prototyping process. It enables rapid production of parts with intricate designs that would be challenging, if not impossible, to fabricate using traditional manufacturing methods. Moreover, it allows us to iterate designs swiftly, leading to quicker turnaround times and significantly accelerating the entire product development timeline.
At Hemargroup, we've leveraged the capabilities of 3D printing to elevate our prototyping process, allowing us to create more accurate and detailed prototypes in less time.
The Power of Diverse 3D Printing Technologies
In our pursuit of prototyping excellence, we utilize various 3D printers and printing technologies, each with their unique strengths, catering to an array of project requirements.
Fused Deposition Modeling (FDM) is often our go-to for robust mechanical parts. FDM works by depositing heated thermoplastic material layer by layer, following a predetermined path. This method is particularly useful for testing parts that need to withstand significant stress or strain, like gears or mounts, due to the strength and durability of the resulting components.
Stereolithography (SLA) offers the ability to create high-resolution components. SLA works by using a laser to harden a liquid resin layer by layer. This technology is excellent for parts that require a smooth finish or intricate detailing, making it ideal for visible components like casings and user interfaces.
Selective Laser Sintering (SLS) comes into play when we're dealing with complex geometries. SLS uses a laser to fuse small particles of plastic, ceramic, or glass, one layer at a time, to produce parts. With this technology, we can create parts with intricate internal structures or ones that require high thermal and chemical resistance.
By harnessing the power of these diverse 3D printing technologies, we ensure that our prototypes not only accurately represent the final product but also provide meaningful data for the refinement and validation process.
3D Printing as a Competitive Edge
In today's fast-paced product development landscape, speed and precision are critical. The ability to quickly iterate designs, test concepts, and refine products provides a significant competitive edge. By incorporating 3D printing into our prototyping process, Hemargroup ensures our clients benefit from accelerated development timelines without compromising on the accuracy or quality of the prototypes.
In essence, 3D printing at Hemargroup is more than just a technology; it's an integral part of our commitment to delivering top-notch, efficient, and reliable prototyping services that exceed client expectations.
The Hemargroup Advantage
The path to a successful product runs through countless iterations, refinements, and rigorous testing, with prototyping as its critical juncture. At Hemargroup, we pride ourselves on the exacting precision and superior quality we bring to every stage of the prototyping process, a commitment that sets us distinctly apart.
A Fusion of Expertise
At the heart of Hemargroup's operation is our interdisciplinary team of seasoned professionals. Our team comprises specialists from various fields, including electronic engineering, mechanical engineering, design, and manufacturing. This rich pool of expertise is the driving force behind our sophisticated and comprehensive approach to prototyping.
Our team members collaborate closely, leveraging their unique insights and experiences to enhance each prototype's functionality, efficiency, and aesthetics. This interdisciplinary approach ensures that every aspect of the product – from circuit layout and mechanical design to user experience and manufacturability – is refined and harmonized, leading to a well-rounded, market-ready prototype.
Rigorous Testing and Quality Checks
At Hemargroup, we firmly believe that the quality of a prototype is a strong indicator of the final product's success. We uphold this belief through a stringent quality assurance process that encompasses rigorous testing and meticulous quality checks.
Every prototype undergoes exhaustive testing to evaluate its performance under various conditions, identify potential issues, and assess its readiness for mass production. These tests can include everything from functionality and stress tests to user experience evaluations, each one designed to ensure the prototype meets our exacting standards of excellence.
Exceeding Expectations: Our Commitment to Clients
The hallmark of our work at Hemargroup is our commitment to not just meet, but exceed, our clients' expectations. Each prototype we create is meticulously crafted and rigorously tested to ensure it embodies our clients' vision while fulfilling the end-users' needs.
By the time a prototype leaves our hands, it has evolved beyond just a proof of concept; it becomes a promise of what's to come in the final product. It stands as a testament to our dedication to delivering top-tier electronic and mechanical design services, offering clients a sneak-peek of the excellence, innovation, and quality they can anticipate in their final product.
The Hemargroup Advantage, in essence, is the assurance of a prototyping partner who understands your vision, caters to your needs, and is committed to turning your ideas into tangible, market-ready products that make a lasting impact.
In Conclusion
At Hemargroup, we believe that a truly exceptional product is the result of a harmonious blend of electronics and mechanics. Through our advanced approach to prototyping, we ensure that every product we create not only performs flawlessly but also provides a seamless and enjoyable user experience. In a world where technology is constantly evolving, our commitment to integrating electronics and mechanics ensures we stay at the forefront of innovative product design.