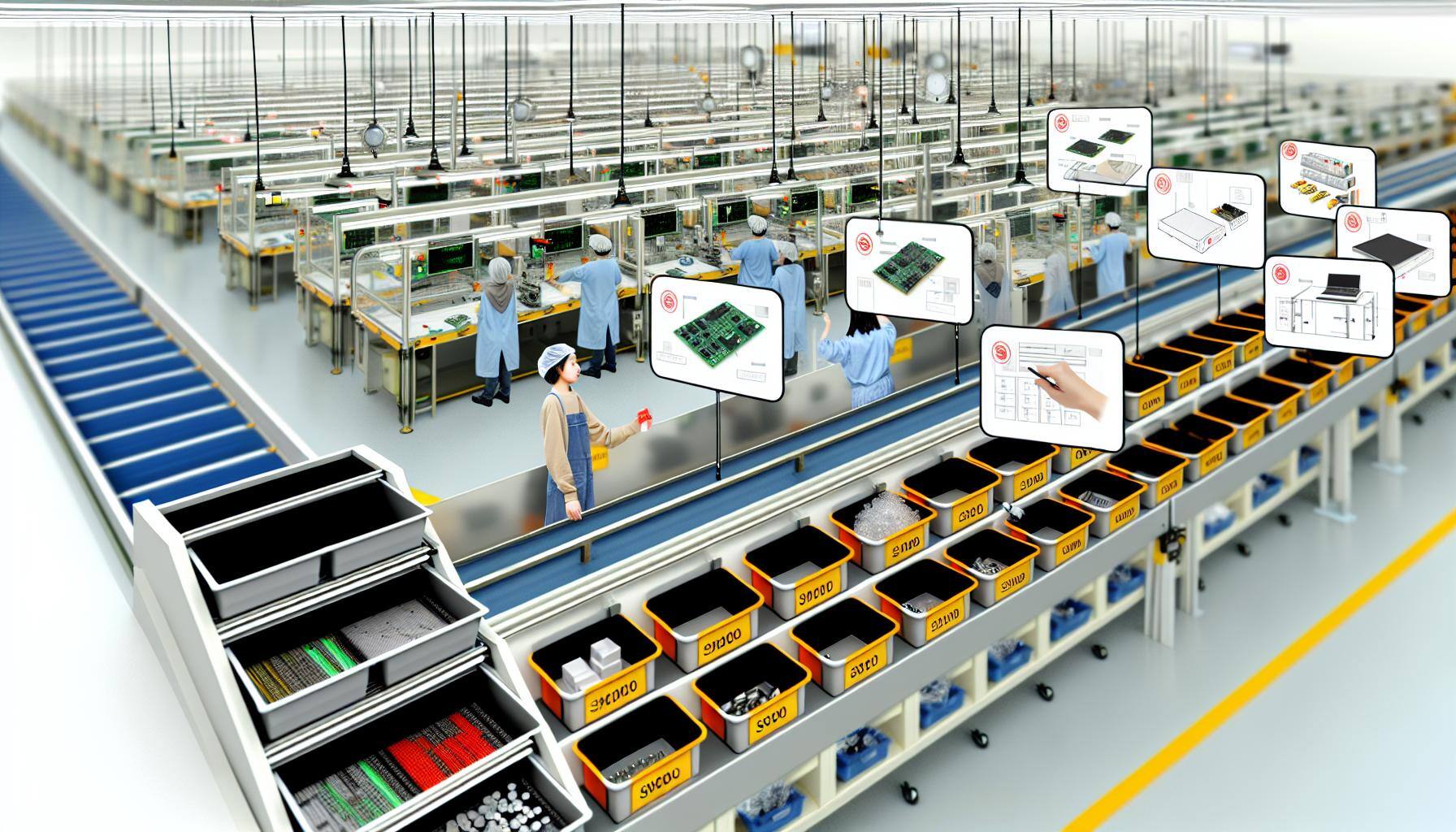
Lean Manufacturing is a methodology that originated in the Japanese automotive industry, with the aim of eliminating waste and optimizing the entire production process. It focuses on increasing efficiency and quality, minimizing waste and operational costs. In the context of Electronic Manufacturing Services (EMS), Lean Manufacturing plays a crucial role in ensuring that processes are fast and maintain consistent quality. In such a dynamic and competitive industry, where products are becoming more complex and market demands are rapidly evolving, adopting a lean approach is essential.
Key Principles of Lean Manufacturing for EMS
-
Waste reduction: The first key principle of Lean Manufacturing is the identification and elimination of waste (muda). In the EMS sector, this waste can take various forms: overproduction, excess inventory, production defects, rework, or downtime. By minimizing these factors, it is possible to make production processes much leaner and more efficient.
-
Continuous improvement (Kaizen): The Kaizen philosophy is central to Lean Manufacturing. It means that every production process is constantly being improved. In EMS, this can translate into small daily improvements that, in the long run, lead to significant benefits in terms of quality and production times.
-
Employee involvement: Another fundamental principle is the involvement of all personnel in improvement processes. In EMS, this means training workers to identify problems and propose solutions, promoting a corporate culture of continuous improvement.
The Benefits of Lean Manufacturing for EMS Services
-
Reduced delivery times: By eliminating waste and streamlining processes, EMS companies can speed up the delivery times of products to customers. In a market where speed is essential, a Lean approach allows companies to remain competitive without compromising quality.
-
Increased quality: The adoption of Lean Manufacturing reduces production errors and rework, improving the final quality of products. For EMS, where even minor defects can cause significant issues in electronic devices' functioning, this is a strategic advantage.
-
Operational efficiency: One of the greatest opportunities offered by Lean Manufacturing is operational efficiency. With simplified processes and fewer resources used inefficiently, production costs are significantly reduced, increasing the company's profitability.
-
Production flexibility: Production lines managed according to Lean principles are more flexible and agile. In a sector like EMS, where customer demands can vary greatly in terms of volume and technical specifications, the ability to adapt quickly is crucial.
Case Study: Application of Lean Manufacturing in Hemargroup
At Hemargroup, the adoption of Lean Manufacturing has had a positive impact on various projects. For example, in the production of a series of electronic boards for a customer in the defense sector, the implementation of Lean principles reduced assembly time by 15%, increased the final product quality, and reduced waste. Thanks to greater process control and complete traceability of each component, Hemargroup has been able to ensure a leaner production process, with on-time deliveries and no rework.
Conclusion
Adopting Lean Manufacturing in EMS services brings numerous benefits: from waste reduction to improved quality, to greater flexibility and production responsiveness. Through the implementation of these principles, Hemargroup positions itself as a reliable and innovative partner for companies seeking operational excellence and competitiveness in the market.