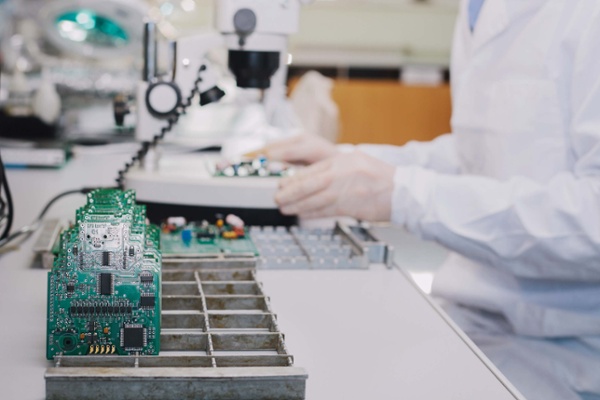
Hemargroup is your go-to contract manufacturing solution. Being an expert for 40+ years in electronic manufacturing services, we have the cutting-edge technology to provide high-end engineering, prototyping, manufacturing, and testing services. We can also adapt to special customer requests.
In this article we will discover our main processes and standardized tests that are made on each PCBA before leaving our plant.
Short on time? Click here to get a personalized quote for your electronic project.
How we manufacture a PCBA?
Manufacturing of Surface Mounted Devices (SMDs) is highly automated and a production monitoring is made on each board.
From supply to testing, here is our 7 step standard PCBA Manufacturing process :
-
The screen printing : the first step of PCB manufacturing is screen printing. The solder paste is put on the printed wiring board in order to create electrical connections. Thanks to our special XL-Screen printing machine, we are able to handle large PCBs, up to a size of 1600mm x 600mm.
-
The solder paste inspection (SPI) : production lines are equipped with 3D optical inspection machines that scan the PCB to verify if the volume of deposited paste complies with the standards. In case of a lack of paste, the entire process is repeated to avoid any failure.
-
Placement of components on PCBs : components listed on the Bill of Materials (BOM) are placed on PCBs by several robot modules. Production lines can be expanded or shortened, depending on the number of components on the PCB. Machines are calibrated to fit the cycle time of the screen printing step.
-
Solder melting : PCBAs go through a tunnel reflow oven with a specific soldering temperature profile, meeting the paste criteria, to melt it and form a solder joint. The temperature increases slowly to avoid thermal shocks that could damage components. The PCBA is then slowly cooled down and the metallic joint solidifies.
-
Soldering Through-Hole (THT) components
Modern PCBA designs focus on the use of surface-mount components (SMD), but in the case of THT components, we use wave soldering machines. In this process, an alloy bath floods the underside of the PCBA instead of using a solder paste.
Another special type of machine, called "selective soldering" can also be used. It’s the evolution of wave soldering. The alloy in this case is brought by a nozzle mounted on a robot that moves between the melting points allowing specific points only to be soldered. -
Automatic optical inspection (AOI) : after each main production process, we have AOI inspection circular stations, which inspect the components and verify that everything is in place on the board. The polarity is verified as well as the size of the solder joint.
-
Double-sided PCBs : for a double-sided assembly, the board is flipped and the entire process starts again. If there are heavy components on the other side, we bond them to prevent falling.
-
Manual operations : the PCBA manufacturing process can’t always be fully automated, especially for “high mix, low volumes”. Some components are complex to assemble requiring manual integration through a soldering iron. Thanks to our skilled staff, we offer a reliable and flexible production chain, which allows us to deal with any quantity and quality requests.
Our Inspection Tests
Final quality check and electrical tests are performed, based on the customer needs, before shipment.
There are two complementary kinds of tests: ICT and FCT. The choice of tests is set up following the customer quality requirements in the upstream design stage.
In-Circuit Test : this type of test is used to verify the components conformity on the board, as per the BOM. It can detect if a single component is defective or outside needed tolerances.
Functional Circuit Test : the functionalities of the PCBA are tested. Hemargroup engineers develop test benches that reproduce the functional aspects of the product. For example, if there is a display, the testing tool verifies that the testing commands display the right information on the screen.
Do you need other services?
In addition to the standard operations, Hemargroup can provide special processes if the customer requires them, which include:
-
Finishing Processes
After inspection tests, the PCBA undergoes special treatments such as conformal coating. This treatment is used to protect the PCBA in humid environments. Furthermore, for confidentiality reasons, Hemargroup can also apply on boards, a black resin coating that can’t be removed. - Final Mounting
Production of the finished good, which involves placing the PCBA in its case and connect any needed cables, buttons, displays and other needed modules. - Packaging and Logistics
Prepare the product for single (B2C) or bulk (B2B) shipments. Using the final product package and delivering the fully functional good to the final customer. - And much more...
Curious to know more about Hemargroup? Are you looking to receive a quote on our electronic manufacturing services? Contact Us: