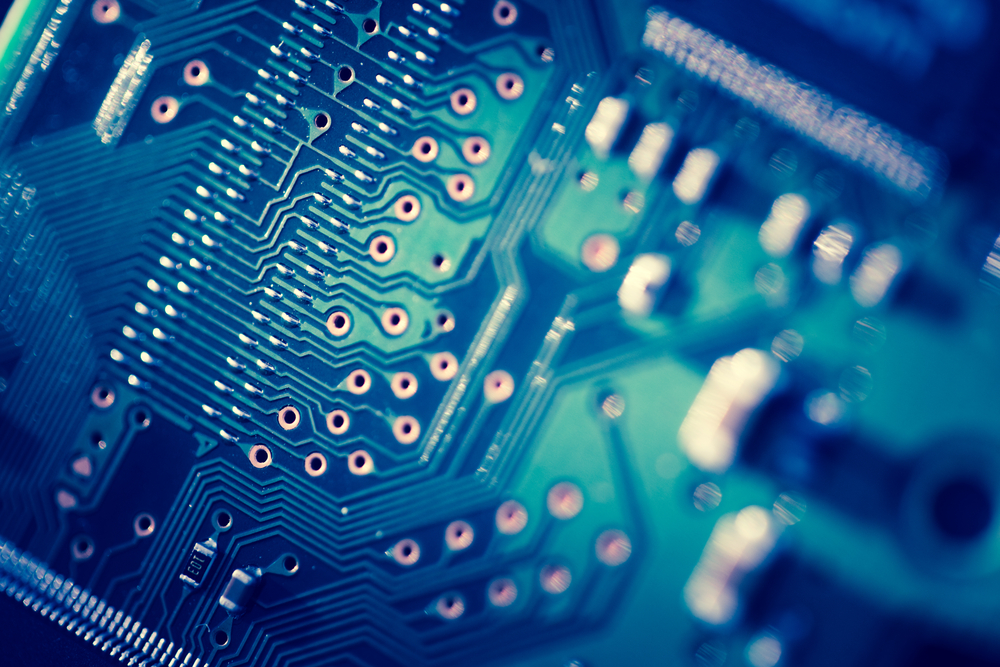
As we have seen before, DFM's goal is to optimize a product with the production phase in mind while still concentrating on its design and engineering. Non-optimized products result in malfunctions, delays and costs, both monetary and in terms of image loss.
Here is a brief step-by-step guide to achieve a successful DFM.
1.Determine the production process
The first step is surely to determine the correct production process for the realization of the product.
This means considering the size of the product, the production run, the necessary materials... It also means considering the primary and secondary steps that the product itself requires, before or after the actual assembly. It can be the engineering department itself to provide an assembly guide to production, with the best processes to obtain the finished product.
2.Optimize the design
Each product has a specific functionality. Optimising its design means not only optimising every single component so that the product guarantees the expected functionality, but also foreseeing the production and assembly steps, to facilitate this passages of the product development journey, reducing errors and downtime.
3.Choose the materials
The materials of a product are also crucial for its proper functioning, especially if it is designed for "special" sectors such as medical or military. There may be specifications for durability, strength or resistance arising from legislation in the sector in which the product operates. In addition, different materials require different production processes, so you should always keep an eye on welding specifications, furnace temperatures, interference and electromagnetic fields... All of which, if neglected, could damage the final product.
4.Identify the environment of use
Parallel to the choice of materials, it is also necessary to consider how and where the final product will be used. As mentioned above, particular sectors such as the military or medical have extremely stringent requirements regarding the qualities that a product must have. A good DFM therefore also takes into account the situations in which the product will be used, so that unfavourable environmental conditions, such as rain, the presence of corrosive or explosive materials, electromagnetic fields, pressures or high altitudes, do not have any impact on the proper functioning of the device produced.
5. Perform the final tests
Like any successful product development process, the final stage involves testing and verifying that the product meets the safety and quality standards of the various authorities. If you rely on third party partners, such as Hemargroup, you will find not only engineering advice on what the safety standards are and how to design the product so that it can pass them without problems, but also the possibility to carry out tests to verify that the product actually meets the standards.
Mistakes to avoid:
In addition to this guide, we would also like to point out what are the most common mistakes, resulting from our experience of over 40 years in this industry.
Hanging around the edges
A very common mistake is not leaving enough spacing between components and the edge of a PCB. If this happens, two things can happen: either the copper of the tracks is not completely covered by the protective coating and corrodes, or during cutting the protective coating is removed. So don't forget to add the right distance between the components and the edge.
Trapping acids
When producing a PCB, you have to be careful how you design the tracks during the routing phase. In fact, it is recommended to avoid making tracks at 90-degree angles, better if at 45 degrees, and especially check if there are any joined tracks. Forgetting these precautions will create acid traps that can damage the PCB.
Complicating the PCB layout
As an old saying goes, "what is not there cannot break". We often see customers and partners providing us with extremely complex, multi-layer board designs with components on both sides of the board.
However, when components are placed on both sides of a PCB, one (or even two) additional production processes are introduced, thereby increasing the cost of production. In addition, the addition of components on both sides of a PCB could add many complications for the manufacturer.
One solution, in this case, could be to change the PCB stack from two to four or even six layers. The added space can facilitate the routing design process and avoid the use of both the top and bottom layers for component placement.
No soldering mask between the pads
Soldering is a very important process in PCB production, as it prevents short circuits and other contact problems.
Make sure you plan this step well, both in the design phase and in the actual production, so that the board has little (or too much) solder paste.
Use the vias in the pads
Using the vias in the component pads is a solution that we often observe, especially in smaller boards. However, we must be very careful, because the reduction of the solder alloy it involves can make the soldering process itself ineffective.
We hope that you like this step by step guide.
If you are looking for a partner who can assist you in the Design for Manufacturing process of your PCB, Contact Us