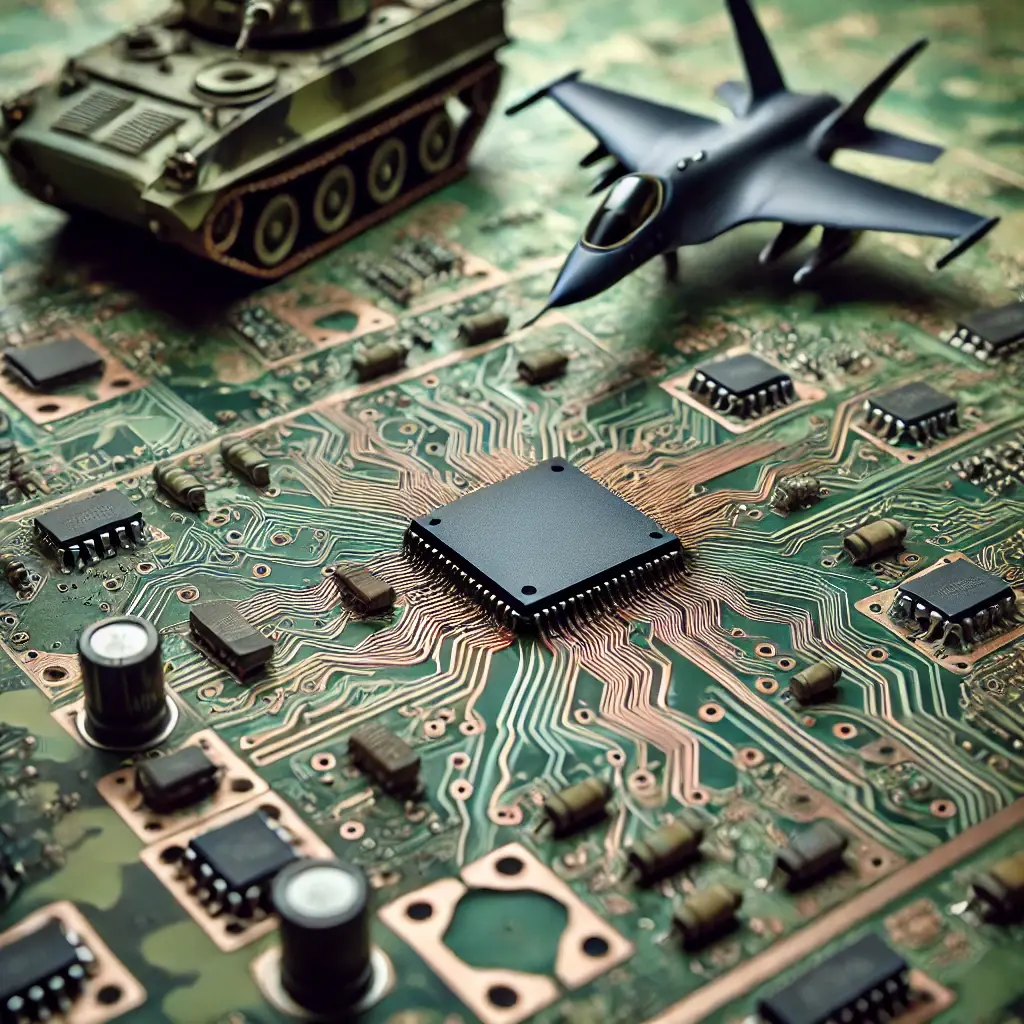
Introduction
Design for Manufacturability (DFM) is a strategic approach that plays a fundamental role in the development of printed circuit boards (PCBs). It optimizes design to facilitate manufacturing processes, reduce costs, and improve overall product reliability. In the context of military PCBs, DFM becomes even more relevant due to the stringent technical requirements, the need for regulatory compliance, and the highly demanding operational environments. In this article, we will explore DFM best practices applied to PCBs intended for military applications, analyzing how the specific characteristics of these devices impose strict design and production criteria.
1. Special Requirements for Military PCBs
PCBs for military applications must operate in environmental and operational conditions far beyond those of standard commercial PCBs. This requires highly robust design to ensure reliability and durability. Key factors to consider include:
-
Extreme Temperatures: Military PCBs must function within a broad temperature range, from -55°C to +125°C, or even higher depending on the operational context, such as war zones or aerospace operations.
-
Shock and Vibration: Devices must withstand constant vibrations and mechanical shocks caused by explosions, emergency landings, or missile launches. The structural robustness of the PCB and its components must be able to handle these stresses without compromising functionality.
-
Electromagnetic Interference (EMI): In military systems, reducing electromagnetic interference is essential to ensure signal clarity and protect against electromagnetic pulse (EMP) attacks. Advanced shielding techniques are often required.
-
Regulatory Compliance: Military PCBs must comply with stringent regulations, such as MIL-PRF-31032 for manufacturing and MIL-STD-810 for environmental durability. These standards define specific guidelines for physical strength, longevity, and environmental compatibility.
2. Choosing Suitable Materials
Material selection is critical in military PCB design, as it directly affects their ability to withstand harsh environmental conditions and operational longevity. Common material options include:
-
High-Performance Substrates: Materials like high Tg (glass transition temperature) FR-4, polyimides, and ceramics offer excellent thermal properties, ensuring that PCBs maintain dimensional stability even in high-temperature environments or in the presence of rapid temperature changes.
-
Durable Surface Finishes: Using finishes like hard gold or nickel-phosphorus is essential for protecting PCB surfaces from corrosion, oxidation, and wear, especially in maritime or space environments.
-
Low Outgassing Materials: In aerospace or satellite applications, it is important that the materials used have low outgassing to prevent contamination of sensors or other critical components.
3. Military-Specific DFM Guidelines for PCBs
Designing reliable and manufacturable military PCBs requires adherence to strict DFM guidelines:
-
Trace Spacing and Layout: In military PCBs, it is advisable to maintain wider spacing between traces to reduce the risk of short circuits and prevent electrical arcing, which could occur in high-voltage or low-pressure conditions.
-
Ground and Power Planes: Separate ground and power planes help improve signal integrity and optimize heat dissipation, reducing the risk of interference and improving power management.
-
Plated Holes and Vias: The use of buried or blind vias can reduce surface complexity and improve reliability. Careful plating of the holes is necessary to avoid defects that could compromise electrical transfer.
4. Assembly Considerations
Assembling military PCBs is as crucial as designing them, as errors during this phase can compromise the operational reliability of the final product:
-
Mil-Spec Components: It is essential to select components that meet military specifications (Mil-Spec) to ensure optimal performance under extreme conditions. These components are tested to withstand shocks, vibrations, temperature variations, and radiation.
-
Advanced Soldering Processes: The use of controlled atmosphere or nitrogen soldering techniques helps prevent oxidation and improves the integrity of solder joints, which is particularly important in military devices exposed to high humidity or corrosive atmospheres.
-
Strict Inspection and Testing: Every PCB destined for military use must undergo rigorous quality control, including functional tests, thermal tests, burn-in tests, and X-ray inspections to detect any manufacturing or soldering defects.
5. Regulations and Certifications
Regulatory compliance is not optional but mandatory for military PCBs. Companies must ensure that every aspect of design and production meets strict military standards:
-
Military Standards: Familiarity with standards such as MIL-STD-810 (environmental testing) and MIL-STD-883 (microelectronic testing) is crucial to ensure that the finished products meet operational expectations.
-
Traceability: Every component and manufacturing process must be carefully documented to ensure full traceability. This allows identification of any defects or variations in the materials used or processes employed.
-
Quality Certifications: Partnering with suppliers that hold certifications such as ISO 9001 or AS9100 is essential to ensure high manufacturing quality standards.
6. Common Challenges and Solutions
In military PCB production, the following challenges are common and require targeted design solutions:
-
Thermal Management: Integrating heat sinks, thermally conductive materials, and heat dissipation planes is critical to prevent component overheating, especially in high-temperature environments.
-
EMI and EMC: Mitigating electromagnetic interference requires careful layout planning, effective shielding, and the use of components certified for EMC (electromagnetic compatibility).
-
Environmental Hardness: Applying conformal coatings or potting can protect PCBs from moisture, dust, contaminants, and extreme vibrations.
Conclusion
DFM design in military PCBs represents a complex challenge that requires advanced expertise and meticulous attention to detail. Following DFM principles can significantly reduce the risk of production failures and ensure that electronic devices meet the most extreme operational demands. To achieve these results, it is essential to collaborate with an experienced EMS (Electronics Manufacturing Services) partner in military PCBs who can guide the project through design, manufacturing, and verification stages in accordance with the strictest military standards.
For more details on how to optimize your military PCB designs or to discuss your specific needs, feel free to contact us.