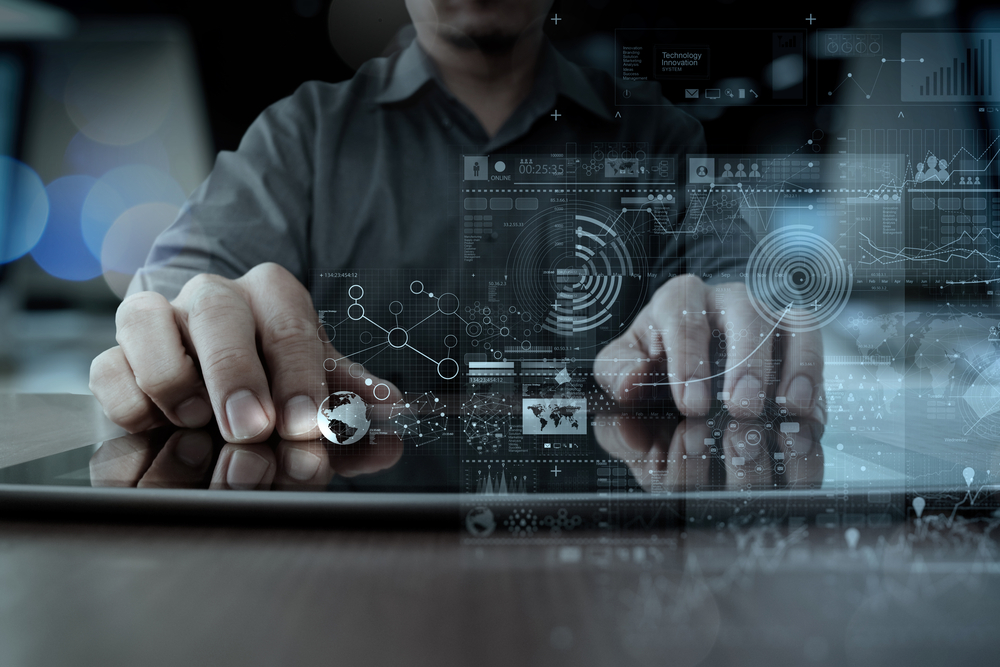
The technological transformation is leading companies into an innovation rush. Innovation is the key point and quickly adopting and adapting to cutting-edge technologies is extremely important. The change over time is so fast that we already talk about industry 5.0, where digitalizing all business areas is just the first step. But how did we come so far with technology? How manufacturing companies can benefit from the transition towards industry 5.0?
Let's do a quick rundown of the transformation from industry 1.0 to the ongoing 5.0, with a particular focus on electronics manufacturing.
The technological transformation: from Industry 1.0 to 5.0
Back in the second half of the 18th century the Industry 1.0 finds its origins with the First Industrial Revolution. The transition to new processes based on water, steam and mechanization brought a lot of benefits for transportation and manufacturing, especially in the textile industry, allowing to produce larger amounts of goods and creating better living conditions. Industry 2.0 started from the first half of the 19th century with the Second Industrial Revolution, occurring mainly in Britain, Germany and in the United States. The society saw the spread of electrical technologies which allowed for even greater production and more sophisticated machines. After a century and a half arrived the Third Industrial Revolution, also referred as the computer era or Industry 3.0, where electronics and IT were the leading players. These technologies led to advanced automated systems in production to perform tasks especially in the assembly, which once were destined to human hands.
Getting near to the contemporary society, the definition of the "Fourth Industrial Revolution" and thus the Industry 4.0 dogma, can be tracked back in 2016 by Klaus Schwab, Founder and Executive Chairman of the World Economic Forum (WEF). It is characterized by the convergence and complementarity of emerging technology domains, including artificial intelligence, nanotechnology, biotechnology, 3D printing, human-machine interfaces, cyber-physical system based on algorithms, the Internet of things (IoT), cloud and cognitive computing. In terms of manufacturing, the industry 4.0 is similar to the concept of the Smart Factory, which is focused on learning and improving by doing, continuously adapting and optimizing its own processes accordingly.
Industry 4.0 has already hugely transformed the global industrial landscape and its technologies are still the dominant ones in the current society even if the industry 5.0 concept is increasingly gaining ground.
Industry 4.0 begins to move towards Industry 5.0 when customers themselves are allowed to customize what they want and where the collaboration between man and machine is enhanced, allowing to find ways to work together to improve the means and efficiency of production. |
Industry 5.0 is not completely new from 4.0 but rather an upgrade of it, focusing on complementary human-machine relationship and leading to the so-called mass customization of products and services thanks to the ultra-fast precision of automated technology with human’s critical thinking skills, supervision and creativity. Rather than pure efficiency in terms of performance and productivity, the goal of Industry 5.0 is the optimization by elevating the quality of production in the manufacturing industry. The concept of Industry 5.0 goes also hand in hand with the model of the circular economy, based on the idea of maximizing efficiency but in line with the minimization of resource inputs, as well as waste and emission production.
Circular economy in the Electronic Manufacturing
The circular economy is an ideal regenerative economic system designed to be efficient in a context where resources are not infinite and which goes towards a gradual transition to renewable resources, and recovery of the materials and products at the end of their life. A lot of companies are increasingly adapting towards this model to face the challenges of the contemporary society and to fulfill sustainability goals. Major drivers of the circular economy which are accelerating the transition towards it are the climate change, global agendas, economic change, job creation, private sector initiatives, new business models, technical development, R&D, natural resources availability change and national legal frameworks. In this sense, digital technologies are useful enablers for the circular economy because they allow to optimize processes and find ways to prolong and redesign the lifecycle of products in the manufacturing industry.
The circular economy in the manufacturing industry can be visually displayed as a never-ending circular process with 5 main steps:
What should you do as a manufacturing company to change and improve your business towards Industry 5.0? Here the main strategic goals of the circular manufacturing economy you should pursue:
Hemargroup's core businesses towards Industry 5.0
At Hemargroup, our goal is to create an environment of innovation and collaboration with our customers. By establishing this type of working relationship, we make it easy for businesses to make the switch to outsourcing without having to worry about any trouble during the transition, while providing a Swiss level of quality and punctuality. By offering a complete portfolio of Electronic Manufacturing Services (EMS), design, engineer, prototype, test, and manufacturing of electronic parts and final products, Hemargroup is in strict control over the full project design & supply journey with its own automated manufacturing under human supervision. The combination of the engineering and production departments allow us to leverage the mass customization which could benefit every kind of project.
The quality and the digitization of our processes is the heart of our strategy and our main goal is to offer the best possible service through the whole product lifecycle. In order to achieve our high standards, we start from the raw materials and components, by periodically visiting our supplier network personally. Our own production site is ISO certified and all processes and procedures are strictly following the IPC guidelines. On top of that, our ISO 13485 and AQAP2110 certifications state our experience in the medical and military secotrs, respecitvely. Finally, the newly acquired ISO 14001 certifies our willingness for a correct environmental management and our efforts for a sustainable product design&production journey.
From the development of your idea up to the mass production of your product, Hemargroup is able to assist you not simply as an EMS supplier but as a reliable partner, ready to grow and develop your project. We are therefore ready to support your needs, but also assist any customer in its European relocation, who is looking for a reliable and solid electronics manufacturing services partner.
Don't hesitate to contact us for more information or to request a quotation on our services.