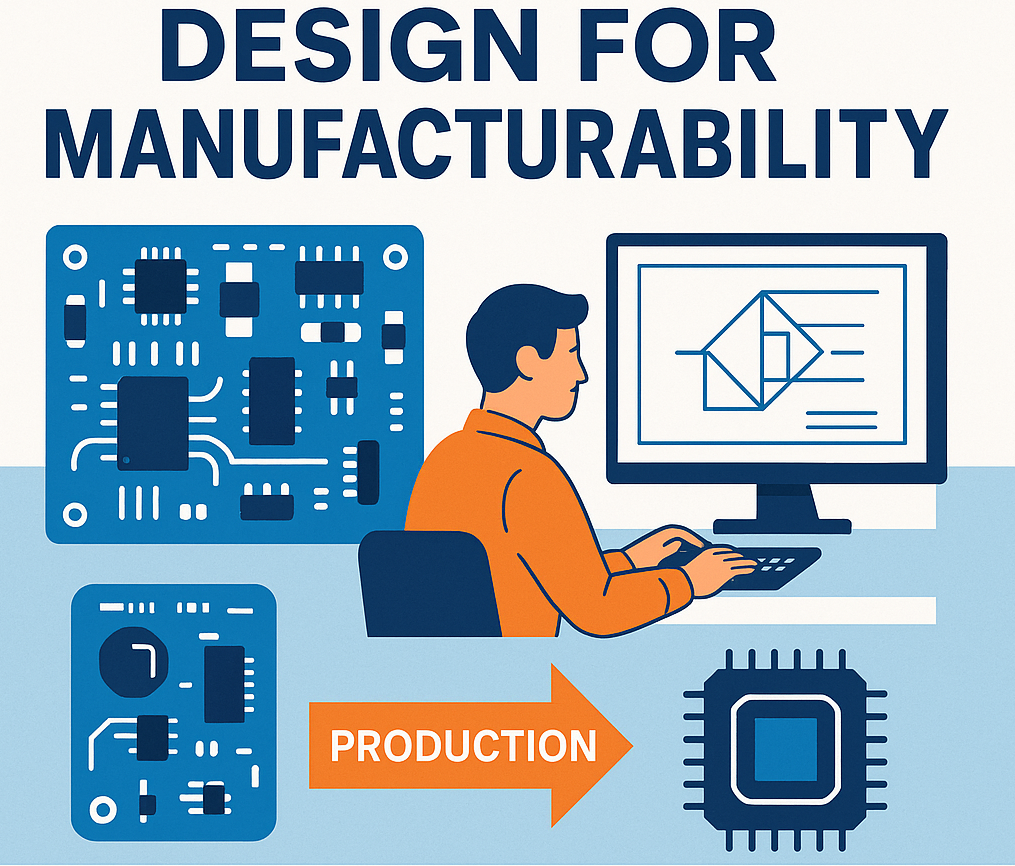
Discover how DFM principles help reduce cost, time, and risk in electronics. Hemargroup applies DFM from day one—design smarter, build faster.
What is Design for Manufacturability (DFM)?
Design for Manufacturability (DFM) is the process of designing products so they are easy and cost-effective to manufacture. It involves anticipating production constraints, minimizing complexity, and ensuring that designs are optimized for real-world fabrication and assembly—right from the start.
In electronic manufacturing, DFM is critical. A poorly designed PCB, even if functional, can result in:
- Higher production costs
- Delays in time-to-market
- Rework and testing failures
- Increased field failure rates
- Damaged brand reputation
Why Every Design Error is Expensive
80% of a product’s cost is determined at the design stage.
Every oversight—wrong footprint, poor component placement, or insufficient tolerance—multiplies exponentially as you move through prototyping, testing, and production.
Phase | Cost of Fixing an Error |
---|---|
Design | $1 |
Prototyping | $10 |
Production | $100 |
Post-market (field) | $1,000+ and reputational damage |
Hemargroup's Approach to DFM in Electronics
At Hemargroup, we integrate DFM principles from day zero—when the first schematics are still on the table.
Our engineering team works closely with clients during the R&D phase to:
- Validate PCB layouts and stack-up
- Optimize for pick-and-place and reflow soldering
- Suggest alternative components to reduce lead time
- Simulate thermal performance and signal integrity
- Review for compliance and testability (DFT)
We are not just contract manufacturers. We are your R&D partner.
Real-World Benefits of Applying DFM
1. Shorter Time-to-Market
Well-designed PCBs go through fewer prototyping iterations and pass tests faster.
2. Lower Production Costs
Reducing manual rework, improving panelization, and using standard footprints all reduce total cost.
3. Higher Product Quality
DFM minimizes variation, improves yield, and increases long-term reliability.
4. Scalability from Prototype to Series
Designs that scale well ensure seamless transition from MVP to mass production.
Common DFM Pitfalls (and How We Help Avoid Them)
Mistake | DFM Solution |
---|---|
Non-standard footprints | We enforce IPC standards |
Components too close to board edge | Design reviews check for mechanical fit |
No test points | We implement DFT from the first revision |
Thermal hotspots | Simulations and layout adjustment |
BOM with EOL or hard-to-source parts | Procurement feedback loop during design |
Partner with Hemargroup Early
Design and manufacturing are two sides of the same coin. The earlier we’re involved in your project, the more value we can provide.
Whether you're working on aerospace, medical devices, consumer electronics or IoT, our integrated engineering and manufacturing model ensures smoother development, faster go-to-market, and long-term product success.
Let’s Talk
Have a project in mind? Want a second opinion on your design?