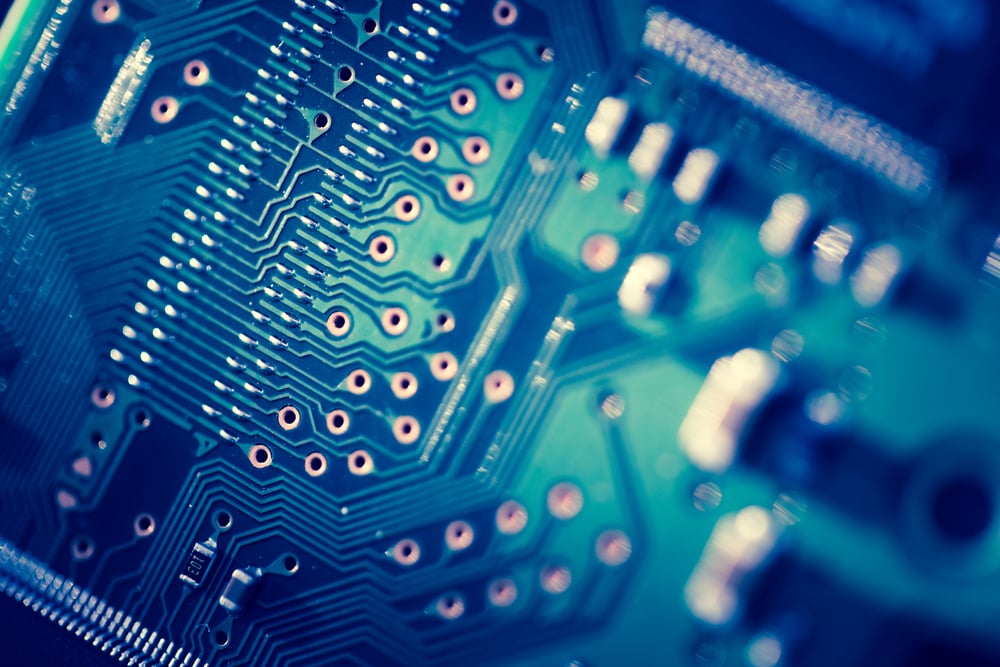
Wie wir bereits gesehen haben, besteht das Ziel von DFM darin, ein Produkt mit Blick auf die Produktionsphase zu optimieren, während man sich weiterhin auf das Design und die Konstruktion konzentriert. Nicht optimierte Produkte führen zu Fehlfunktionen, Verzögerungen und Kosten, sowohl in finanzieller Hinsicht als auch im Hinblick auf den Imageverlust.
Hier ist eine kurze Schritt-für-Schritt-Anleitung, um ein erfolgreiches DFM zu erreichen.
1.den Produktionsprozess bestimmen
Der erste Schritt ist sicherlich die Bestimmung des richtigen Produktionsprozesses für die Realisierung des Produkts.
Das bedeutet, die Größe des Produkts, die Produktionsserie, die notwendigen Materialien zu berücksichtigen... Es bedeutet auch, die primären und sekundären Schritte zu berücksichtigen, die das Produkt selbst erfordert, vor oder nach der eigentlichen Montage. Es kann die Engineering-Abteilung selbst sein, die einen Montageleitfaden für die Produktion mit den besten Verfahren zur Erzielung des Endprodukts bereitstellt.
2. die Konstruktion optimieren
Jedes Produkt hat eine spezifische Funktionalität. Die Optimierung seines Designs bedeutet nicht nur die Optimierung jedes einzelnen Bauteils, so dass das Produkt die erwartete Funktionalität garantiert, sondern auch die Produktions- und Montageschritte vorauszusehen, um diese Passagen der Produktentwicklung zu erleichtern und Fehler und Ausfallzeiten zu reduzieren.
3.die Materialien auswählen
Die Materialien eines Produkts sind ebenfalls entscheidend für sein einwandfreies Funktionieren, insbesondere wenn es für "spezielle" Sektoren wie den medizinischen oder militärischen Bereich bestimmt ist. Es kann Spezifikationen für Haltbarkeit, Festigkeit oder Widerstandsfähigkeit geben, die sich aus der Gesetzgebung in dem Sektor ergeben, in dem das Produkt funktioniert. Darüber hinaus erfordern unterschiedliche Materialien auch unterschiedliche Produktionsprozesse, so dass Sie Schweißspezifikationen, Ofentemperaturen, Interferenzen und elektromagnetische Felder stets im Auge behalten sollten... All diese Faktoren könnten, wenn sie vernachlässigt werden, das Endprodukt beschädigen.
4.die Einsatzumgebung identifizieren
Parallel zur Wahl der Materialien muss auch überlegt werden, wie und wo das Endprodukt eingesetzt werden soll. Wie bereits erwähnt, stellen bestimmte Sektoren wie das Militär oder die Medizin äußerst strenge Anforderungen an die Eigenschaften, die ein Produkt haben muss. Ein gutes DFM berücksichtigt daher auch die Situationen, in denen das Produkt eingesetzt werden soll, so dass ungünstige Umgebungsbedingungen wie Regen, das Vorhandensein von korrosiven oder explosiven Materialien, elektromagnetische Felder, Druck oder große Höhen keine Auswirkungen auf das einwandfreie Funktionieren des hergestellten Geräts haben.
5. Führen Sie die abschließenden Tests durch
Wie bei jedem erfolgreichen Produktentwicklungsprozess wird in der letzten Phase geprüft und verifiziert, ob das Produkt den Sicherheits- und Qualitätsstandards der verschiedenen Behörden entspricht. Wenn Sie sich auf Drittpartner wie die Hemargroup verlassen, finden Sie hier nicht nur technische Beratung zu den Sicherheitsnormen und zur Gestaltung des Produkts, damit es diese ohne Probleme erfüllen kann, sondern auch die Möglichkeit, Tests durchzuführen, um zu überprüfen, ob das Produkt tatsächlich den Normen entspricht.
Fehler, die es zu vermeiden gilt:
Zusätzlich zu diesem Leitfaden möchten wir auch auf die häufigsten Fehler hinweisen, die sich aus unserer über 40-jährigen Erfahrung in dieser Branche ergeben.
An den Rändern hängen
Ein sehr häufiger Fehler ist es, nicht genügend Abstand zwischen Komponenten und dem Rand einer Leiterplatte zu lassen. Wenn dies passiert, können zwei Dinge passieren: Entweder wird das Kupfer der Leiterbahnen nicht vollständig von der Schutzschicht bedeckt und korrodiert, oder beim Schneiden wird die Schutzschicht entfernt. Vergessen Sie also nicht, den richtigen Abstand zwischen den Bauteilen und der Kante hinzuzufügen.
Säure-Fallen
Wenn Sie eine Leiterplatte herstellen, müssen Sie während der Routing-Phase sorgfältig darauf achten, wie Sie die Leiterbahnen entwerfen. Es wird empfohlen, Leiterbahnen nicht in 90-Grad-Winkeln zu entwerfen, besser in 45-Grad-Winkeln, und vor allem zu prüfen, ob es verbundene Leiterbahnen gibt. Das Vergessen dieser Vorsichtsmaßnahmen führt zu Säurefallen, die die Leiterplatte beschädigen können.
Komplizierung des PCB-Layouts
Wie ein altes Sprichwort sagt: "Was nicht da ist, kann nicht zerbrechen". Wir sehen oft Kunden und Partner, die uns äußerst komplexe, mehrschichtige Leiterplattendesigns mit Bauteilen auf beiden Seiten der Leiterplatte liefern.
Wenn jedoch Komponenten auf beiden Seiten einer Leiterplatte platziert werden, werden ein (oder sogar zwei) zusätzliche Produktionsprozesse eingeführt, wodurch sich die Produktionskosten erhöhen. Darüber hinaus könnte das Hinzufügen von Komponenten auf beiden Seiten einer Leiterplatte viele Komplikationen für den Hersteller mit sich bringen.
Eine Lösung könnte in diesem Fall darin bestehen, den PCB-Stapel von zwei auf vier oder sogar sechs Kupfer-Lagen zu ändern. Der zusätzliche Platz kann den Routing-Designprozess erleichtern und die Verwendung sowohl der oberen als auch der unteren Lage für die Komponentenplatzierung vermeiden.
Keine Lötmaske zwischen den Pads
Das Löten ist ein sehr wichtiger Prozess in der Leiterplattenproduktion, da es Kurzschlüsse und andere Kontaktprobleme verhindert.
Stellen Sie sicher, dass Sie diesen Schritt gut planen, sowohl in der Entwurfsphase als auch in der eigentlichen Produktion, so dass die Leiterplatte wenig (oder zu viel) Lötpaste enthält.
Positionierung der "Vias" in den Pads
Die Verwendung der Durchkontaktierungen in den Komponenten-Pads ist eine Lösung, die wir häufig beobachten, insbesondere bei kleineren Platinen. Wir müssen jedoch sehr vorsichtig sein, denn die damit verbundene Reduzierung der Lötlegierung kann den Lötprozess selbst uneffektiv machen.
Wir hoffen, dass Ihnen diese Schritt-für-Schritt-Anleitung gefallen hat.
Wenn Sie auf der Suche nach einem Partner sind, der Sie beim Designprozess für die Produktion Ihrer Leiterplatte unterstützen kann, kontaktieren Sie uns:
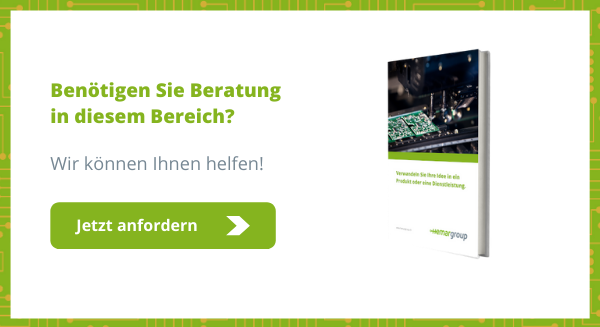