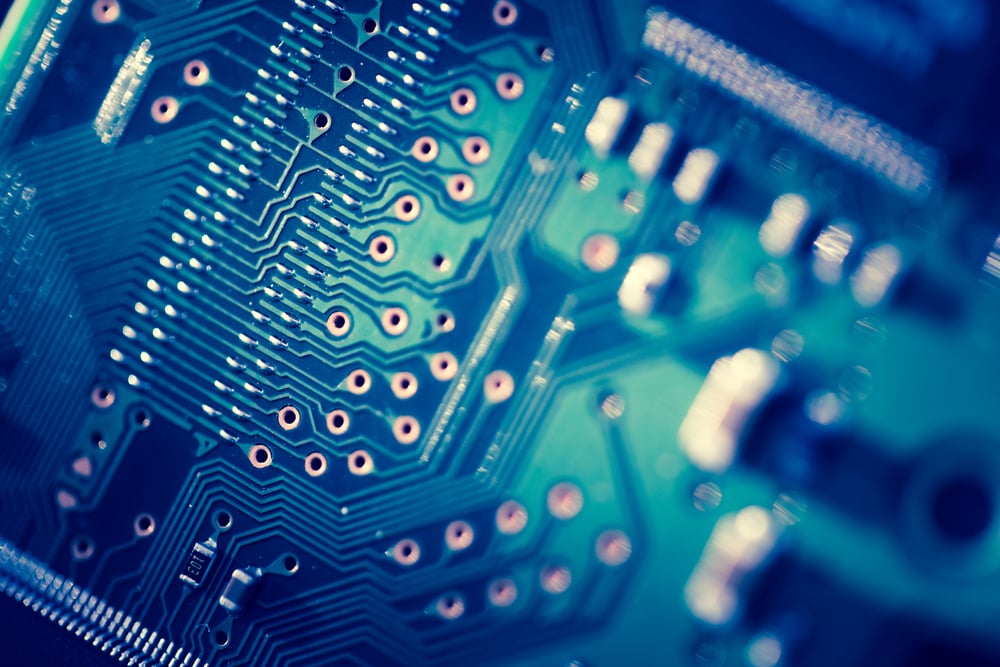
Come abbiamo visto in precedenza, l'obiettivo del DFM è quello di ottimizzare un prodotto pensando già alla fase di produzione quando si è ancora concentrati nel design ed engineering dello stesso. Prodotti non ottimizzati risultavano in malfunzionamenti, ritardi e costi, sia monetari che in termini di perdite di immagine.
Ecco quindi una breve guida, step by step, dei passi da fare per ottenere un DFM di successo.
1.Determinare il processo di produzione
Il primo step è sicuramente quello di determinare il corretto processo produttivo per la realizzazione del prodotto.
Questo significa considerare le dimensioni del prodotto, la tiratura, i materiali necessari... Significa anche considerare i passaggi primari e secondari che richiede il prodotto stesso, prima o dopo l'assemblaggio vero e proprio. Può essere lo stesso reparto di ingegneria a fornire una guida di assemblaggio alla produzione, con i processi migliori per ottenere il prodotto finito.
2.Ottimizzare il design
Ogni prodotto ha una funzionalità specifica. Ottimizzarne il design significa non soltanto ottimizzare ogni singola componente affinchè il prodotto garantisca le funzionalità previste, ma anche prevederne i passaggi di produzione e assemblaggio, per facilitare questo passaggio del product development journey, riducendo errori e tempi morti.
3.Scegliere i materiali
Anche i materiali di un prodotto sono cruciali per il suo corretto funzionamento, in particolare se è pensato per settori "particolari" quali il medicale o il militare. Possono esserci specifiche in merito alla durata, solidità o resistenza derivanti dalla legislazione del settore nel quale il prodotto opera. Inoltre, materiali diversi richiedono processi produttivi diversi, pertanto occorre sempre dare un occhio alle specifiche di saldatura, alle temperature dei forni, a interferenze e campi elettromagnetici... Tutte cose che, se trascurate, potrebbero danneggiare il prodotto finale.
4.Identificare l'ambiente di utilizzo
Parallelamente alla scelta dei materiali, occorre considerare anche come e dove verrà utilizzato il prodotto finale. Come detto in precedenza, settori particolari come il militare o il medicale hanno delle necessità estremamente stringenti in merito alle qualità che un prodotto deve avere. Un buon DFM tiene quindi conto anche delle situazioni in cui il prodotto verrà utilizzato, in modo che condizioni ambientali sfavorevoli, quali ad esempio pioggia, presenza di materiali corrosivi o esplosivi, campi elettromagnetici, pressioni o altitudini elevate, non abbiano alcun impatto sul corretto funzionamento del dispositivo prodotto.
5. Eseguire i test finali
Come ogni processo di sviluppo di un prodotto che si rispetti, la fase finale riguarda i test e la verifica che il prodotto soddisfi gli standard di sicurezza e di qualità delle varie autorità preposte. Se vi affidate a partner di terze parti, come Hemargroup, troverete non soltanto la consulenza ingegneristica su quali sono gli standard di sicurezza e come disegnare il prodotto affinché possa superarli senza problemi, ma anche la possibilità di effettuare i test per verificare l'effettiva adeguatezza del prodotto rispetto agli standard.
Gli Errori da evitare:
In aggiunta a questa guida, ci piacerebbe anche segnalare quelli che sono gli errori più comuni, derivanti dalla nostra esperienza di oltre 40 anni nel settore.
Addossarsi ai bordi
Un errore molto comune è quello di non lasciare abbastanza distanziamento tra i componenti e il bordo di un PCB. Se questo avviene, possono accadere due cose: o il rame delle piste non è totalmente ricoperto dal rivestimento protettivo e si corrode, oppure durante il taglio il rivestimento protettivo viene rimosso. Non dimenticate perciò di aggiungere la giusta distanza fra componenti e bordo.
Intrappolare gli acidi
Nella produzione di un PCB, bisogna fare attenzione a come si progettano le tracce durante la fase di routing. È infatti consigliato di evitare di fare tracce ad angoli di 90 gradi, meglio se a 45 gradi, e sopratutto controllare qualora ci siano delle tracce unite. Dimenticare questi accorgimenti creerà delle trappole per gli acidi che possono danneggiare il PCB.
Complicare il layout del PCB
Come recita un vecchio detto: "ciò che non c'è non può rompersi". Vediamo spesso clienti e partner fornirci dei design di schede estremamente complessi, multi-strato e con componenti su entrambi i lati della scheda.
Tuttavia, quando si collocano i componenti su entrambi i lati di un PCB, si introduce uno (o anche due) processi di produzione in più, aumentando di conseguenza il costo di produzione. Inoltre, l'aggiunta di componenti su entrambi i lati di un PCB potrebbe aggiungere numerose complicazioni per il produttore.
Una soluzione, in questo caso, potrebbe essere quella di cambiare lo stack di PCB da due a quattro o addirittura sei strati. Lo spazio aggiunto può facilitare il processo di progettazione del routing ed evitare l'uso sia dello strato superiore che di quello inferiore per il posizionamento dei componenti.
Nessuna maschera di saldatura tra i pad
La saldatura è un processo molto importante nella produzione di PCB, in quanto previene i cortocircuiti e altri problemi di contatto.
Assicuratevi di pianificare bene questo passaggio, sia nella fase di design che nell'effettiva produzione, in modo che la scheda non abbia poca (o troppa) pasta saldante.
Utilizzare i via nei pad
Utilizzare i via nei pad dei componenti è una soluzione che osserviamo spesso, sopratutto nelle schede più piccole. È una soluzione però a cui bisogna fare molta attenzione, poichè la diminuzione della lega saldante che essa comporta, può rendere inefficace il processo di saldatura stesso.
Ci auguriamo che questa guida passo dopo passo vi sia piaciuta.
Se siete alla ricerca di un partner che vi possa assistere nel processo di progettazione per la produzione del vostro PCB, contattateci